On May 7, 2025, FlashPhos hosted a hybrid workshop at Dyckerhoff’s cement plant, exploring a promising and complex question: how can phosphorus recovery be effectively integrated into the cement industry? This question brought together experts from research, engineering, and cement production to discuss process synergies in the context of circular economy, decarbonisation, and resource efficiency.
The central focus of the workshop was on FlashPhos slag, a by-product of the thermochemical recycling of sewage sludge, and its potential use as a raw material in cement production. Additionally, the integration of fuel gases produced during the FlashPhos process into cement kilns was critically discussed in terms of both opportunities and challenges.
Following a welcome by Marcus Paul (Dyckerhoff), Christian Schmidberger (University of Stuttgart) gave an overview of the FlashPhos process, highlighting its potential alignment with cement plant infrastructure. The process doesn’t only recover white phosphorus but also produces mineral-rich slag and high-temperature gas streams, opening the door for industrial symbiosis.
In his presentation, Marcus Paul emphasised the transformation underway in the cement and concrete sectors: from reducing CO₂ emissions to rethinking raw material inputs and entire process chains. He presented early-stage results on the activity index of cements blended with FlashPhos slag, which showed promising performance characteristics.
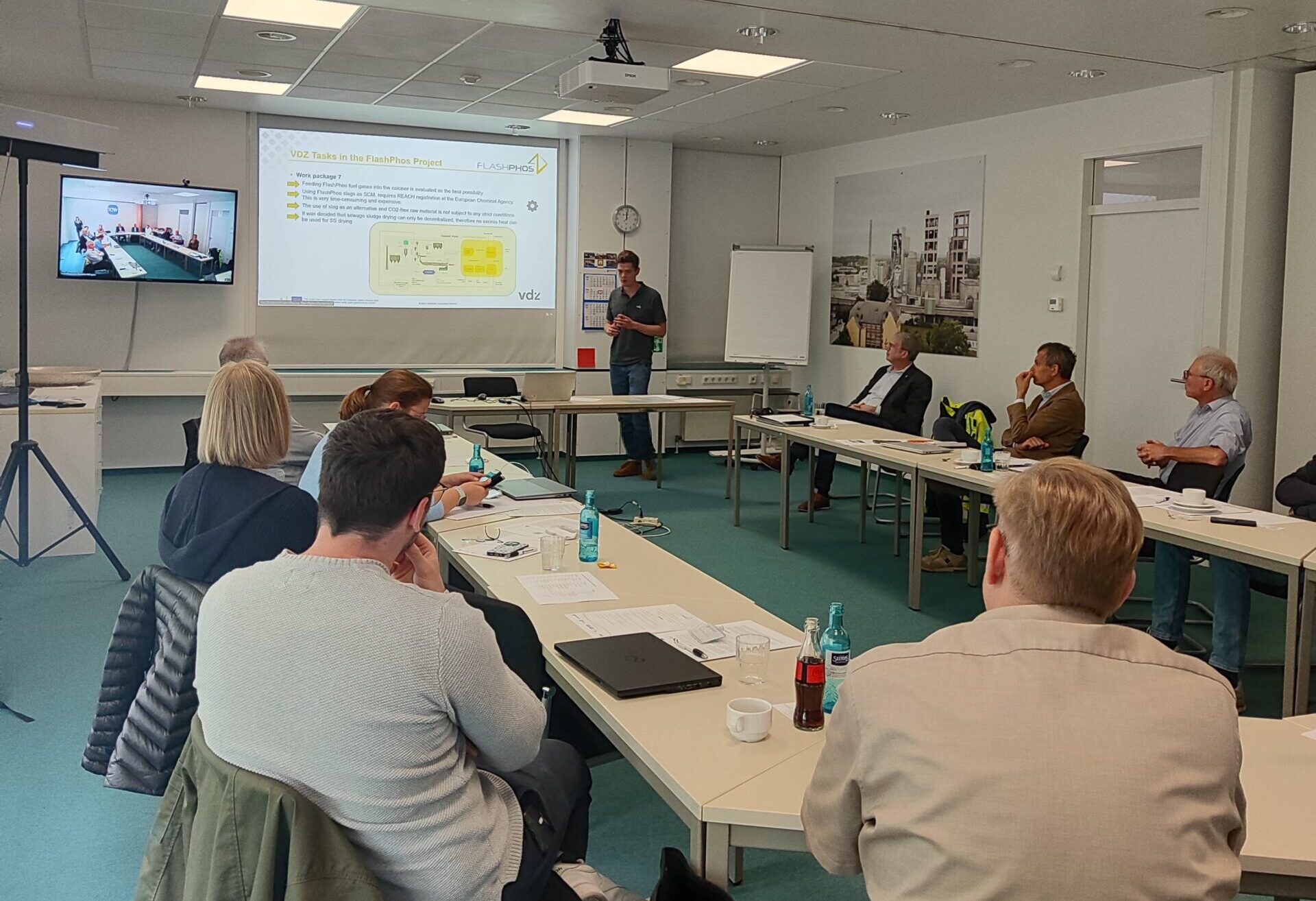
Stefan Papkalla (VDZ), representing the German cement industry, provided a deep dive into the thermodynamic and operational implications of integrating FlashPhos fuel gases. He explained that for phosphorus production of 5,000 tonnes per year, very high fuel gas flows rate can be expected. The resulting excess heat – especially at lower gas temperatures – must be reused efficiently, for example in sewage sludge drying, to avoid additional CO₂ emissions. However, if the fuel gases are considered renewable, CO₂ emissions coming from the conventional fuels could be reduced significantly
Sabrina Frühauf (A TEC) highlighted the company’s role in bridging FlashPhos with cement pyroprocessing, emphasizing A TEC’s expertise in integrating alternative gas flows and materials into clinker production. She presented a holistic approach to CO₂ reduction and shared sustainable engineering examples, including carbon capture, utilization, and storage (CCUS) strategies.
The open discussion after the presentations brought lively exchange. Topics ranged from using FlashPhos off-gas for calcining clay, to introducing organic waste into the hot gas stream for hydrogen production. Participants also debated how best to position FlashPhos within the broader waste management and circular economy framework – not just as a phosphorus recovery solution, but as a multi-benefit technology.
Economic factors were also on the table: current market prices for white phosphorus, cost considerations for sewage sludge treatment, and energy input requirements. The central takeaway was that integration must be designed with process synergies in mind – from energy reuse to material compatibility. Scientific models and industrial realities must be aligned for successful large-scale implementation.
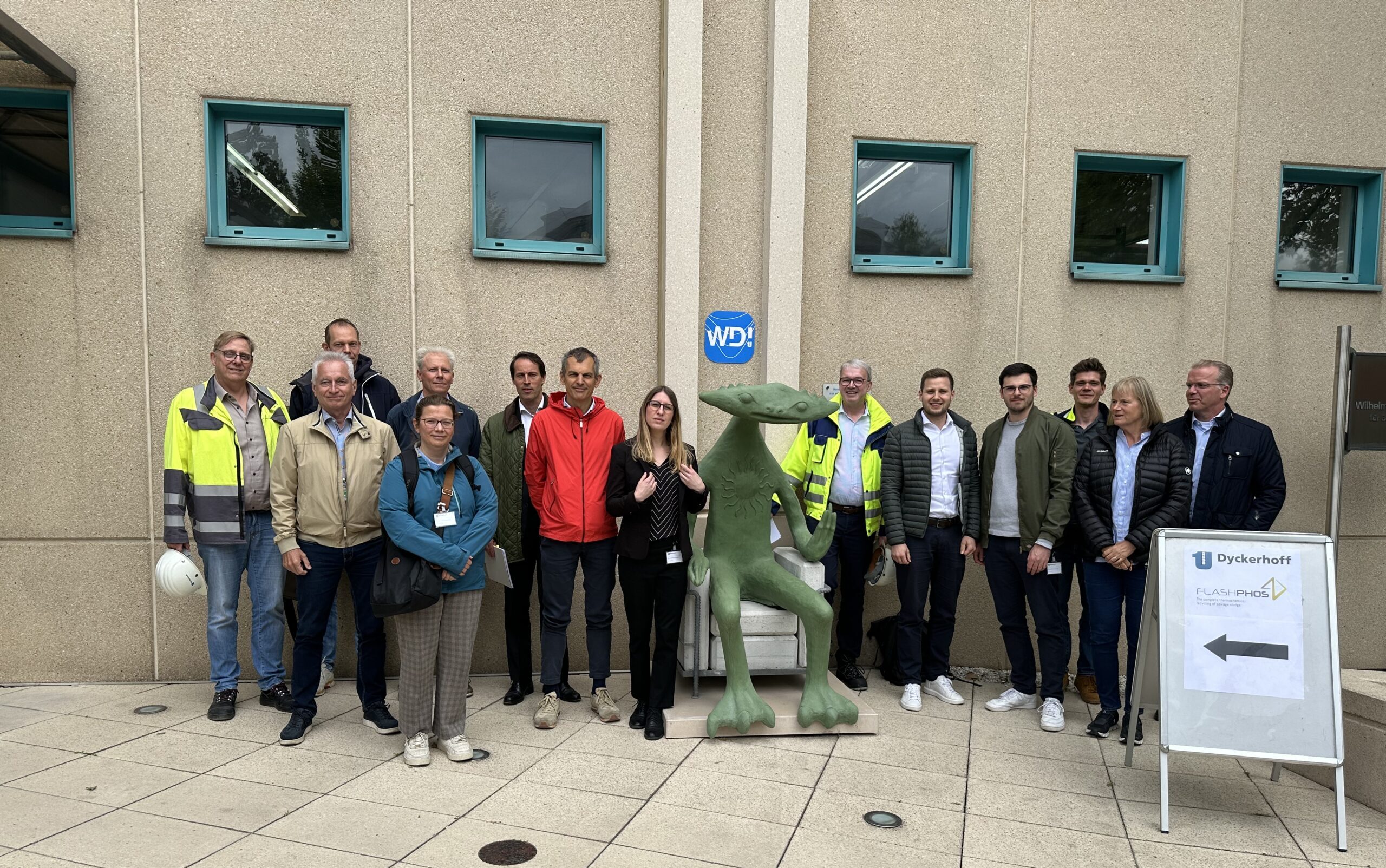
The workshop concluded with a guided plant tour at Dyckerhoff, where participants gained direct insight into the cement production process and potential integration points for the FlashPhos concept.
The event was jointly organized by Dyckerhoff, Steinbeis Europa Zentrum, VDZ Technology gGmbH, A TEC Production and Services GmbH and Italmatch Chemicals.
For further information contact
Christian Schmidberger
Researcher & FlashPhos Project Coordinator
University of Stuttgart, Institute of Combustion and Power Plant Technology
christian.schmidberger@ifk.uni-stuttgart.de